Przemysł metalurgiczny odgrywa kluczową rolę w gospodarce każdego kraju, ponieważ dostarcza niezbędnych surowców do wielu innych branż. Metalurgia zajmuje się przetwarzaniem metali oraz ich stopów, co pozwala na uzyskanie materiałów o pożądanych właściwościach fizycznych i chemicznych. W ramach tego przemysłu wyróżniamy różne etapy produkcji, począwszy od wydobycia surowców mineralnych, przez ich obróbkę, aż po wytwarzanie gotowych produktów. Warto zauważyć, że przemysł metalurgiczny jest niezwykle zróżnicowany i obejmuje zarówno produkcję stali, jak i metali nieżelaznych, takich jak miedź czy aluminium. Dzięki zastosowaniu nowoczesnych technologii, procesy metalurgiczne stają się coraz bardziej efektywne i ekologiczne. Współczesny przemysł metalurgiczny dąży do minimalizacji wpływu na środowisko poprzez recykling materiałów oraz wdrażanie innowacyjnych rozwiązań technologicznych.
Jakie są główne procesy w przemyśle metalurgicznym?
W przemyśle metalurgicznym wyróżniamy kilka kluczowych procesów, które są niezbędne do uzyskania wysokiej jakości produktów metalowych. Pierwszym z nich jest wydobycie surowców mineralnych, które stanowią podstawę dla dalszych etapów produkcji. Surowce te są następnie poddawane różnym procesom obróbczo-przetwórczym, takim jak topnienie, odlewanie czy walcowanie. Topnienie metali polega na ich ogrzewaniu do odpowiedniej temperatury, co pozwala na uzyskanie ciekłej formy metalu. Kolejnym ważnym etapem jest formowanie, które może przybierać różne formy, takie jak odlewy czy blachy. Po uformowaniu metale często wymagają dalszej obróbki mechanicznej, aby uzyskać pożądane kształty i właściwości. Procesy te mogą obejmować cięcie, gięcie czy spawanie. Ostatnim krokiem w produkcji jest zazwyczaj obróbka cieplna lub chemiczna, która ma na celu poprawę właściwości mechanicznych oraz odporności na korozję gotowych wyrobów.
Jakie są najważniejsze zastosowania metali w różnych branżach?
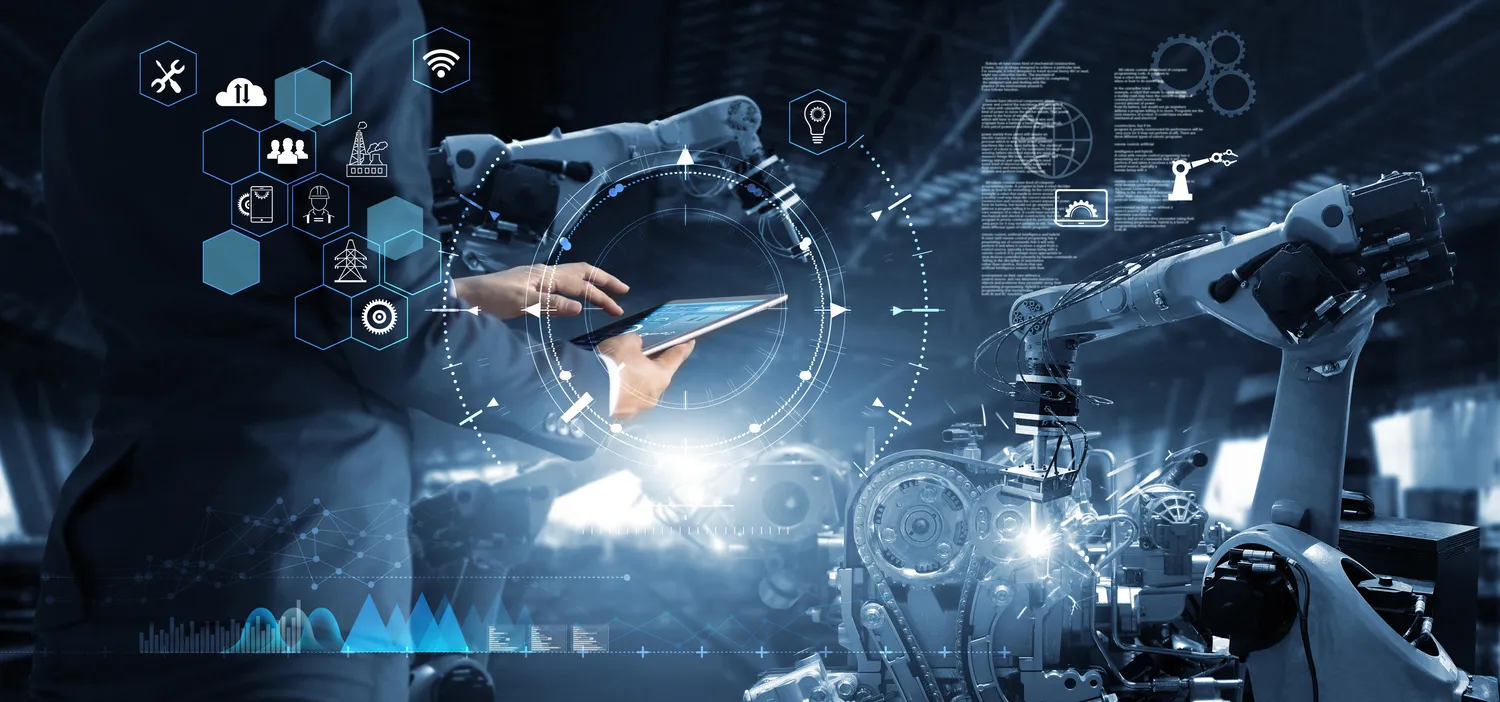
Metale mają szerokie zastosowanie w różnych branżach przemysłu oraz codziennym życiu. W budownictwie stal jest jednym z najczęściej wykorzystywanych materiałów ze względu na swoją wytrzymałość oraz elastyczność. Stalowe konstrukcje nośne są fundamentem wielu budynków oraz mostów, co czyni ją niezastąpionym materiałem w tej dziedzinie. W motoryzacji metale takie jak aluminium i stal są kluczowe dla produkcji pojazdów. Aluminium jest cenione za swoją lekkość oraz odporność na korozję, co przyczynia się do zwiększenia efektywności paliwowej samochodów. W elektronice metale przewodzące, takie jak miedź i złoto, są niezbędne do produkcji układów elektronicznych oraz kabli. Dodatkowo metale szlachetne znajdują zastosowanie w jubilerstwie oraz jako elementy dekoracyjne. W przemyśle chemicznym metale są wykorzystywane jako katalizatory w różnych reakcjach chemicznych.
Jakie wyzwania stoją przed przemysłem metalurgicznym?
Przemysł metalurgiczny stoi przed wieloma wyzwaniami związanymi z globalnymi trendami oraz zmianami technologicznymi. Jednym z głównych problemów jest konieczność dostosowania się do rosnących wymagań dotyczących ochrony środowiska. Zwiększona świadomość ekologiczna społeczeństwa sprawia, że przedsiębiorstwa muszą inwestować w technologie zmniejszające emisję gazów cieplarnianych oraz zużycie energii. Recykling metali staje się coraz bardziej istotny jako sposób na ograniczenie wydobycia surowców naturalnych oraz redukcję odpadów. Kolejnym wyzwaniem jest konkurencja ze strony krajów rozwijających się, które często oferują tańsze produkty dzięki niższym kosztom pracy oraz surowców. Przemysł metalurgiczny musi również stawić czoła problemom związanym z dostępnością surowców mineralnych oraz ich cenami na rynkach światowych. Inwestycje w badania i rozwój nowych technologii są kluczowe dla utrzymania konkurencyjności oraz innowacyjności tego sektora.
Jakie są najnowsze technologie w przemyśle metalurgicznym?
W ostatnich latach przemysł metalurgiczny przeszedł znaczące zmiany dzięki wprowadzeniu nowoczesnych technologii, które zwiększają efektywność produkcji oraz poprawiają jakość wyrobów. Jednym z kluczowych trendów jest automatyzacja procesów produkcyjnych, która pozwala na zminimalizowanie błędów ludzkich oraz zwiększenie wydajności. Roboty przemysłowe są coraz częściej wykorzystywane do wykonywania powtarzalnych zadań, takich jak spawanie, cięcie czy pakowanie. Wprowadzenie sztucznej inteligencji i analizy danych umożliwia optymalizację procesów produkcyjnych oraz przewidywanie awarii maszyn, co przekłada się na mniejsze przestoje i oszczędności. Kolejnym innowacyjnym rozwiązaniem jest zastosowanie technologii druku 3D, która pozwala na tworzenie skomplikowanych struktur metalowych w krótszym czasie i przy mniejszym zużyciu materiału. Druk 3D znajduje zastosowanie w prototypowaniu oraz produkcji małoseryjnej, co daje możliwość szybkiego reagowania na potrzeby rynku. Technologie takie jak spawanie laserowe czy plazmowe również zyskują na popularności, ponieważ umożliwiają precyzyjne łączenie metali o różnych właściwościach.
Jakie są perspektywy rozwoju przemysłu metalurgicznego?
Perspektywy rozwoju przemysłu metalurgicznego są obiecujące, zwłaszcza w kontekście rosnącego zapotrzebowania na metale w różnych sektorach gospodarki. W miarę jak świat staje się coraz bardziej zrównoważony, oczekuje się, że przemysł metalurgiczny będzie musiał dostosować swoje procesy do wymogów ekologicznych. W związku z tym rozwój technologii recyklingu oraz wykorzystania surowców wtórnych stanie się kluczowym elementem strategii wielu firm. Ponadto rosnąca liczba inwestycji w badania i rozwój nowych stopów metali o lepszych właściwościach otworzy nowe możliwości dla innowacyjnych produktów. Przemysł metalurgiczny będzie również musiał stawić czoła wyzwaniom związanym z cyfryzacją i automatyzacją, co może prowadzić do zmiany struktury zatrudnienia oraz wymagań dotyczących umiejętności pracowników. Wzrost znaczenia technologii informacyjnych w zarządzaniu procesami produkcyjnymi może przyczynić się do zwiększenia efektywności i redukcji kosztów operacyjnych. Wreszcie globalizacja rynku metali sprawi, że firmy będą musiały konkurować nie tylko ceną, ale także jakością swoich produktów oraz innowacyjnością rozwiązań.
Jakie są różnice między metalami żelaznymi a nieżelaznymi?
W przemyśle metalurgicznym metale dzielimy na dwie główne kategorie: metale żelazne i nieżelazne, które różnią się pod względem właściwości fizycznych, chemicznych oraz zastosowań. Metale żelazne, takie jak stal i żelazo, charakteryzują się wysoką wytrzymałością oraz twardością, co sprawia, że są idealne do budowy konstrukcji nośnych oraz elementów mechanicznych. Stal jest stopem żelaza z węglem i innymi pierwiastkami, co pozwala na uzyskanie różnych właściwości w zależności od składu chemicznego. Metale żelazne są podatne na korozję, dlatego często stosuje się je w połączeniu z powłokami ochronnymi lub poprzez procesy galwanizacji. Z kolei metale nieżelazne, takie jak miedź, aluminium czy cynk, mają niższą gęstość oraz lepszą odporność na korozję. Miedź jest doskonałym przewodnikiem elektryczności i ciepła, co czyni ją niezastąpioną w elektronice i energetyce. Aluminium jest lekkim metalem o dużej odporności na korozję, dlatego znajduje szerokie zastosowanie w przemyśle lotniczym oraz motoryzacyjnym.
Jakie są najważniejsze surowce wykorzystywane w metalurgii?
W przemyśle metalurgicznym kluczową rolę odgrywają surowce mineralne, które stanowią podstawę dla produkcji metali i ich stopów. Najważniejszym surowcem wykorzystywanym do produkcji stali jest ruda żelaza, która zawiera tlenki żelaza i inne minerały. Proces wydobycia rudy żelaza polega na jej eksploatacji z kopalni oraz poddaniu dalszej obróbce w piecach hutniczych. Oprócz rudy żelaza istotnymi surowcami są również koks oraz wapno, które służą jako materiały pomocnicze podczas procesu produkcji stali. Koks jest paliwem wykorzystywanym do ogrzewania pieców hutniczych i redukcji tlenków żelaza do postaci czystego metalu. W przypadku metali nieżelaznych kluczowymi surowcami są miedź (wydobywana głównie z rud miedzi), aluminium (pozyskiwane z boksytu) oraz cynk (uzyskiwany z rudy cynkowej). Surowce te przechodzą różnorodne procesy obróbcze przed ich finalnym wykorzystaniem w produkcji komponentów metalowych.
Jakie są skutki działalności przemysłu metalurgicznego dla środowiska?
Działalność przemysłu metalurgicznego ma istotny wpływ na środowisko naturalne, co wiąże się zarówno z procesami wydobycia surowców mineralnych, jak i ich przetwarzania. Wydobycie rudy żelaza czy innych metali często prowadzi do degradacji terenów naturalnych oraz utraty bioróżnorodności. Procesy te mogą generować znaczne ilości odpadów górniczych oraz pyłów zawieszonych, które mogą negatywnie wpływać na jakość powietrza i zdrowie ludzi mieszkających w pobliżu kopalni. Ponadto podczas produkcji metali emitowane są gazy cieplarniane oraz inne substancje szkodliwe dla atmosfery, co przyczynia się do zmian klimatycznych oraz problemów zdrowotnych związanych z zanieczyszczeniem powietrza. W odpowiedzi na te wyzwania wiele firm podejmuje działania mające na celu minimalizację negatywnego wpływu swojej działalności na środowisko poprzez wdrażanie nowoczesnych technologii oczyszczania gazów czy systemów zarządzania odpadami. Recykling metali staje się coraz bardziej popularny jako sposób na ograniczenie zużycia surowców naturalnych oraz zmniejszenie emisji związanych z ich wydobyciem i przetwarzaniem.